
How do self-drilling fasteners work?
- Read time: 3 minutes
- Date: 14 Dec 2021
- Flat Roofing
- Rainscreen & Façades
- Sheeting & Cladding
This removes the need to drill a hole prior to using a self-tapping fastener or rivet.
Below is a list of common fastener features and their role in fastener performance. Features may vary depending on the application.

The fastener head has several functions – during installation, the head shape corresponds exactly with the drive tool being used, so the fastener can be driven into place. Some of the most commonly used heads used in construction are hexagon, pan and countersunk.
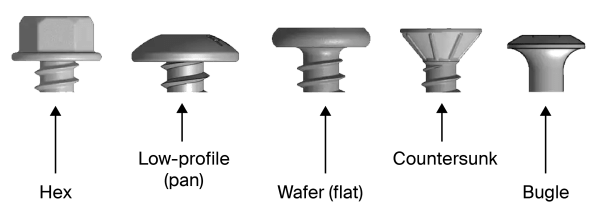
Once the fastener has been correctly installed, the head clamps the material in place and contributes to its pull-over value/performance.
What are fastener performance values?
Fastener heads also have an aesthetic purpose. As a result, they may have a low-profile or be coloured to match the material they are securing. Some of our fasteners also have a moulded nylon head.
Where a weatherproof seal is required there is normally a bonded washer beneath the fastener head.
The drillpoint must be hard enough to create a hole in the substrate. For this reason, stainless steel self-drilling fasteners have carbon steel drillpoints welded to the body of the fastener. This hardened drillpoint pierces and taps into the metal substrate, pre-forming the material for the stainless thread.
Find out how self-drilling fasteners are made
Different types of drillpoint are used depending on the thickness of the steel substrate being fastened into. The length of the drillpoint will vary depending on the thickness of the material it is penetrating. The pilot (unthreaded) section of the fastener must be long enough to drill right through the material before the thread engages. Premature thread engagement can lead to fastener failure.
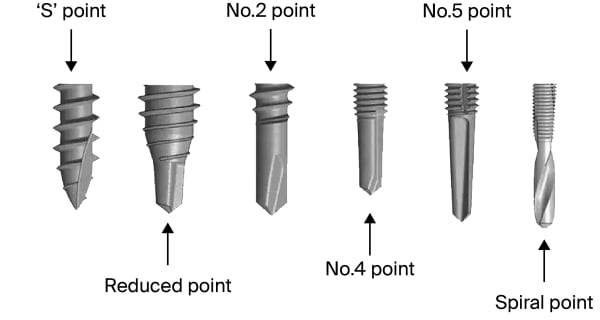
The drill flute is part of the drillpoint and is designed to remove swarf (drilled material) from the drill hole. This is important because the swarf contains up to 80% of the heat generated during the drilling process and contact with high temperatures can cause the point to overheat and fail.
The thread is designed to engage in the substrate to ensure the material is fastened securely. Different styles and shapes of thread are used depending on the application, which would include the thickness of the steel substrate and the material being secured.
Wings are added to fasteners used for securing wood to steel. They are positioned just behind the drill point to create a clearance hole that prevents the timber from riding up (known as jacking up) the fastener during the drilling process. The wings are precisely calibrated to break off on contact with the steel substrate, allowing the thread to tap and secure the material in place.
Free-spin zones are used to prevent over-driving and thread stripping in thin materials while creating an effective weatherproof seal.
Find out why you need a free-spin on a stitching fastener
High threads are used on fasteners designed to fix composite panels to steel and timber. The high thread is positioned under the head of the fastener and has the same pitch as the main thread but with a larger diameter. This creates a positive clamping force to the top sheet of the panel, which ensures the weatherproof seal is maintained should the panel be compressed for example by foot traffic.