
3 years of British manufacturing
- Read time: 3 minutes
- Date: 17 Jan 2024
3 years ago we unveiled the UK's first and most advanced manufacturing facility for fasteners. With a strong commitment to British design and quality, our promise for products that perform has never wavered - and here we are today, 3 years on from the first steps we took with a 4.0 aerospace-grade manufacturing cell.
What does having an advanced manufacturing cell mean for our customers?
Our whole focus is around giving the right advice to choose the right product, to get the product to the right place, at the right time. Essentially: you get what you need when you need it.
How does the UK manufacturing facility assist that?
We have full control over the manufacturing process from design right through to delivery, so every fastener is precisely manufactured to our specification
Being in the UK means reduced lead times for manufactured parts
Our R&D facility gives us the ability to prototype bespoke fastener designs to suit our OEM partners specifications and problem solve challenges facing the industry - faster than ever before
A functioning 4.0 'Industry-first' grade facility allows us to monitor each stage of the manufacturing process and give us data on the cell - so we can produce fasteners with greater speed and more technical accuracy than ever before
Ultimately, our focus is to ensure the quality of the products we design and manufacture are the best they can possibly be, so they always exceed the expectations of our customers.
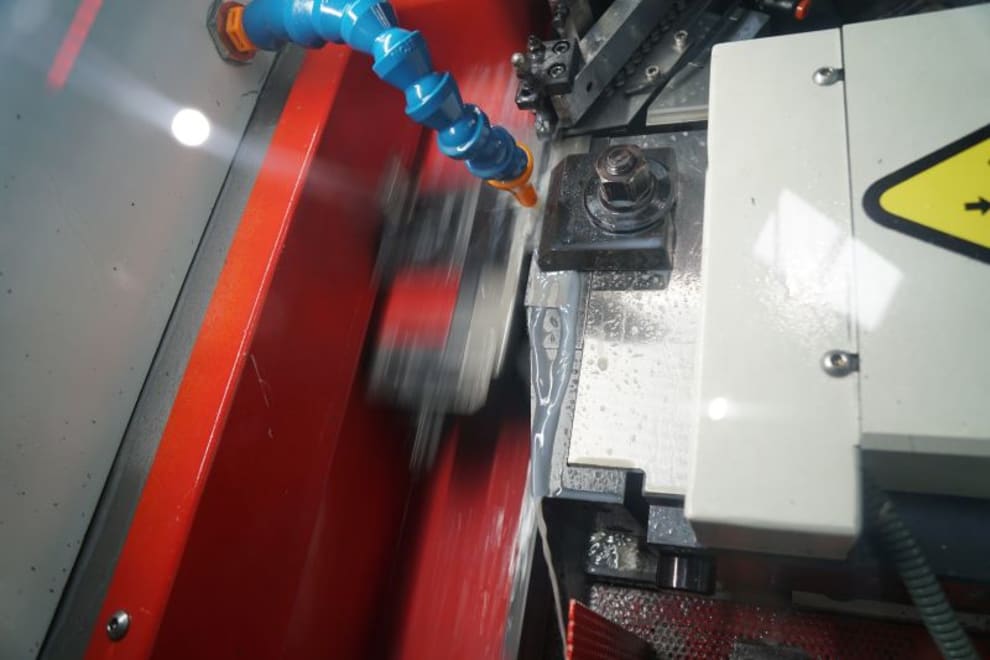
What's happened with the manufacturing facility since 2021?
Our manufacturing facility has allowed us to completely understand the limits, and therefore the full potential, of fastener manufacturing - like improved real-world durability, consistency of performance, or pull-out design. That's how we're achieving manufacturing excellence and evolving already good products into great product products.
But 'becoming better' is something we stand by here at Fixfast. Industry leaders are always looking for incremental improvements to what they do, and our UK R&D cell is the power behind how we achieve that at Fixfast. It allows us to know exactly where and how to make continuous improvements, over time.
We've been able to break down every individual design aspect of each fastener to truly understand what makes that important to the customer. We've challenged all the old best practices in terms of fastener design, material choice, thread form, etc. We've gone back to basics to ask 'why is that the best thing to do?' - and if we don't have a good answer to that question, that's when R&D kicks in. How could we do it differently? Is there extra benefit for the customer to be gained here?
It's about taking that product as far as you can with modern manufacturing techniques.
There's an important environmental consideration too. Having extra UK manufacturing capacity reduces our need for international shipping which slashes lead times for customers and cuts Fixfast's carbon footprint.
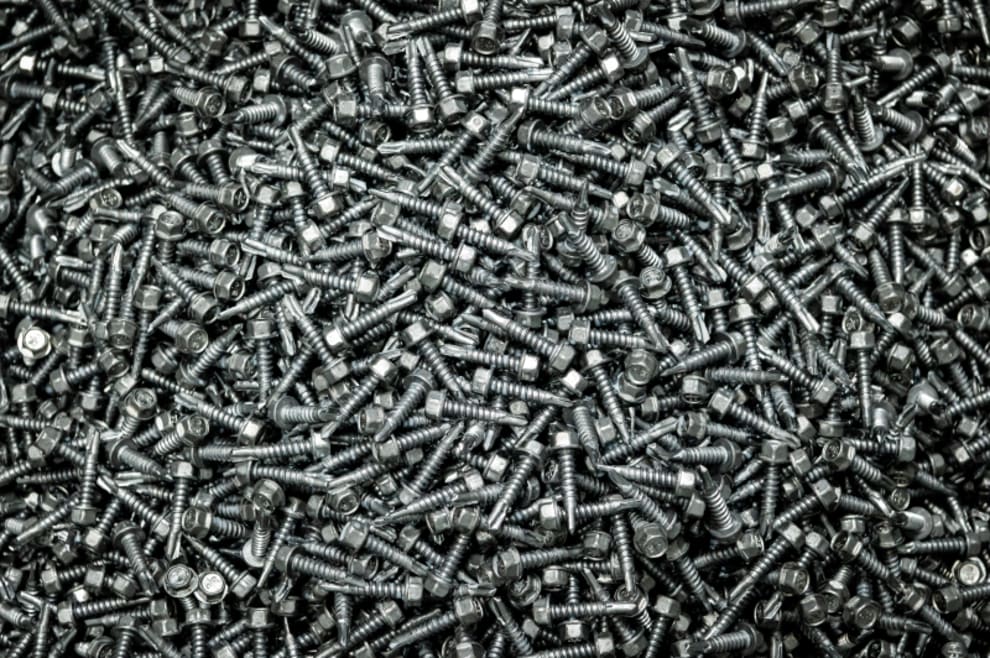
The future of innovation and R&D for fasteners
Looking to the future, we anticipate even more potential for innovative, high-performance fasteners.
It's fair to say that our manufacturing focus will increasingly extend beyond quality and precision, to the opening up of new design possibilities.
A significant proportion of our R&D is in partnership with the larger system OEMs. As they develop new systems for the envelope, perhaps using new materials or enabling modern methods of construction, there's often a need to develop a bespoke fastener to fully complement that system. Our facility means we can produce working prototypes within a matter of days.
That manufacturing agility has also proven important to OEMs that have a need for a niche, but still, essential, fastener solution. Our ability to retool our production lines quickly means, unlike some other manufacturers, we don't have to hold partners to a restrictive minimum order quantity. Without that flexibility from their manufacturing partner, it would be more difficult for those new systems to be brought to market - and ultimately, we'd see stifled innovation in the sector.